Our research contributes design and fabrication technology for composite
materials, especially for carbon fiber reinforced polymeric composite (CFRP).
Versatile multi-scale simulations are performed in the Koyanagi Laboratory,
including multi-time scale simulation (time hominization analysis). Density
functional theory (DFT), Molecular orbital (MO), Molecular dynamics (MD),
Smoothed particle hydrodynamics (SPH), Computational fluid dynamics (CFD),
and Finite element method (FEM) are employed to simulate various phenomena
of CFRP. FEM is our major simulation method. Corresponding experiments
are carried out to verify the simulated results are true. Key point of
our research is considering how nano-scale phenomena and macro-scale phenomena
are linked properly. All the research are being implemented with some contracts.
If you would have some interests, please do not hesitate to access us.
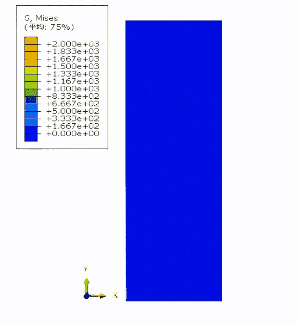
In order to secure the continuous use of CFRP, we aim to predict residual
strength and lifetime quantitatively, assuming the thermodynamic entropy
as the measure of microscopic damage and fatigue. Though CFRP becomes common
material for transport vehicle, it has been difficult to estimate the lifetime
because of complex response of composite materials and structure. We apply
“Entropy-damage”-involved viscoelastic-viscoplastic constitutive relationship
to resin properties in CFRP, and then understand various time-dependent
and multi-scale failures of CFRP through the comparison of experimental
and numerical results. Such microscopic damages and degradation are validated
by molecular simulation linked to the entropy damage model. This study
will enable the simulation of failure under multiple loadings and fatigue
for composite material.
A spacecraft departing from the Earth has to reduce its kinetic energy
when it returns to or reaches its destination planet; otherwise, it may
pass over without orbiting the planet or it may collide with the planet.
This is because a certain amount of kinetic energy is necessary to leave
the gravisphere of the earth. On planets with an atmosphere, thermal energy
is generated by friction between the atmosphere and the spacecraft; in
other words, kinetic energy is converted into thermal energy and the spacecraft
slows down allowing it to arrive safely at its destination. Of course,
the spacecraft may also burn up when leaving or reentering the atmosphere,
a basic principle in the field of aerospace. Koyanagi Laboratory performs
studies on protection from heat generated when spacecraft enter the atmosphere
of Mars and Earth. We design the heat shield for re-entering spacecraft,
the evaluation of its heat resistance, its thermal analysis, and the evaluation
of the insulation material. We perform collaborative investigations with
Japan Aerospace Exploration Agency (JAXA), so that the student in charge
of this theme in a doctoral or master's thesis will continue to work on
such research as a trainee of JAXA.
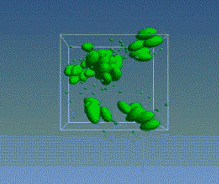
In order to design materials from an atomistic view point, we study molecular
dynamics. Our studies focus on interface bonding, graphene composites,
liquid crystals, drag delivery, biomimetics, and so on. Koyanagi Laboratory
is a key member of the molecular dynamics research group that is affiliated
to the Japan Society for Composite Materials. The research group holds
regular meetings every 3 months and we broadcast each meeting through the
WebEx system. If you are interested in knowing more about our group, please
contact us anytime.
An energy director (ED), a sharp, flat- or triangular-shaped resin bead,
is usually inserted between CFRPs during ultrasonic welding. In this study,
a two-dimensional model was used to conduct finite element analyses for
CFRP ultrasonic welding. The effects of the ED shape on the temperature
increase, deformation history, and dissipated energy behavior are discussed.
The results of the numerical simulations show that the triangular ED more
easily increases the temperature than the flat ED does, and thus its use
consumes less energy and time than using the flat ED. However, this study
indicates that a triangular ED is not always better than a flat ED. In
the ED, the temperature is distributed significantly; that is, the temperature
range between points is vast. There is the possibility that unexpected
chemical reactions such as oxidation occur. It is found that an abrupt
temperature increase is caused by a synergic effect. That is, the increase
in temperature causes the viscoelastic and frictional dissipated energy
to be remarkable, and an increase in dissipated energy increases the temperature.
Consequently, it is difficult to optimize the parameters, such as overall
pressure, frequency, and welding time, for ultrasonic welding.